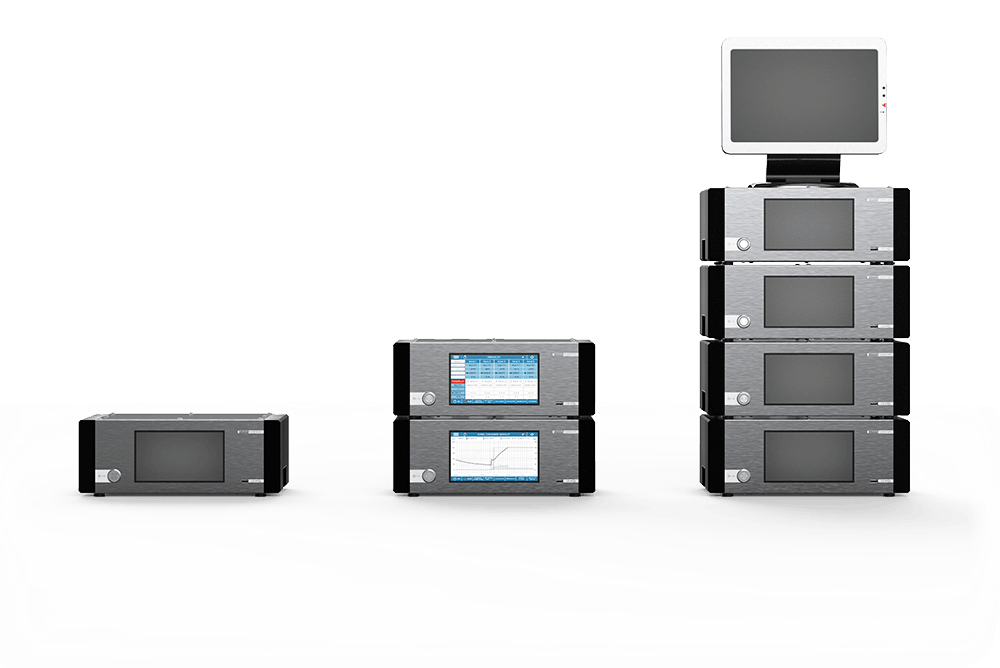
Hot runner controller with user-friendly & modern device concept
⇨ For precise temperature control and predictive control
The THERMONOM hot runner controller has a new, intuitive device concept that ensures precise temperature detection, the fastest switching processes, predictive control and several protective functions for the hot runner molds. A microprocessor controls the channels independently of each other, but can also combine them into synchronized groups.
Based on a network approach, several devices can be linked together via Ethernet and operated as a single, large functional unit. It can be operated from each individual device, from an industrial PC or from the process control station.
A new cost-effective approach
Current hot runner controllers for plastics processing must be able to cover applications with just one to more than 100 channels, which usually requires the development of different sizes of control technology.
The THERMONOM hot runner controller is available in a single size with optimum component utilization and minimum weight and space requirements. By networking several devices and a license model, any number of channels can be achieved.
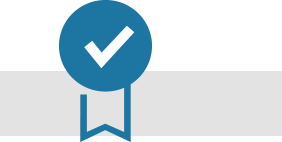
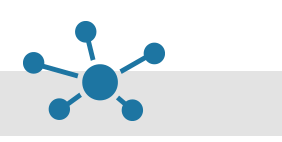
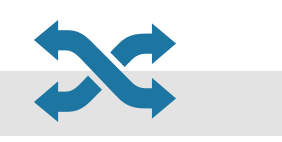
Characteristics of the THERMONOM hot runner controller
REVERSE POLARITY PROTECTION
The THERMONOM hot runner controller detects incorrectly connected temperature sensors
PID CONTROLLER
- Optimized PID controller with automatic adaptation
- Synchronization of multiple, flexibly groupable control zones
FANLESS DESIGN
Fanless design of the hot runner controller, with convective cooling of the power electronics
EXTREMELY COMPACT SIZE
- Robust housing construction, anodized aluminium and stainless steel 1.4301 (V2A)
- Barely larger than a DIN A4 page, weight 6.5 kg
INTUITIVE USER INTERFACE
- Clear user interface on 7″ touch display
- Resolution 800 x 480 pixels
FAST CONFIGURATION
- Wizard – quick configuration when changing tools
- Diagnostic function for toolmakers and setters
The user interface
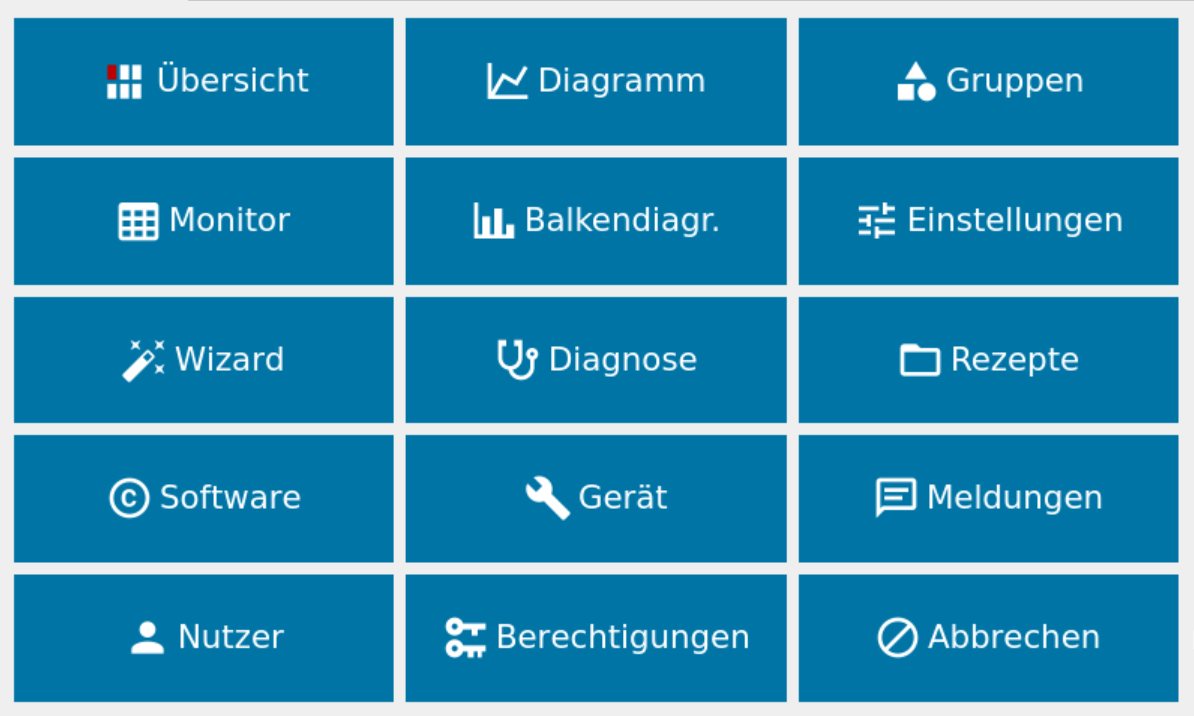
MAIN MENU
Direct access to all functions. Critical device settings of the hot runner controller can be protected against incorrect operation by user control.
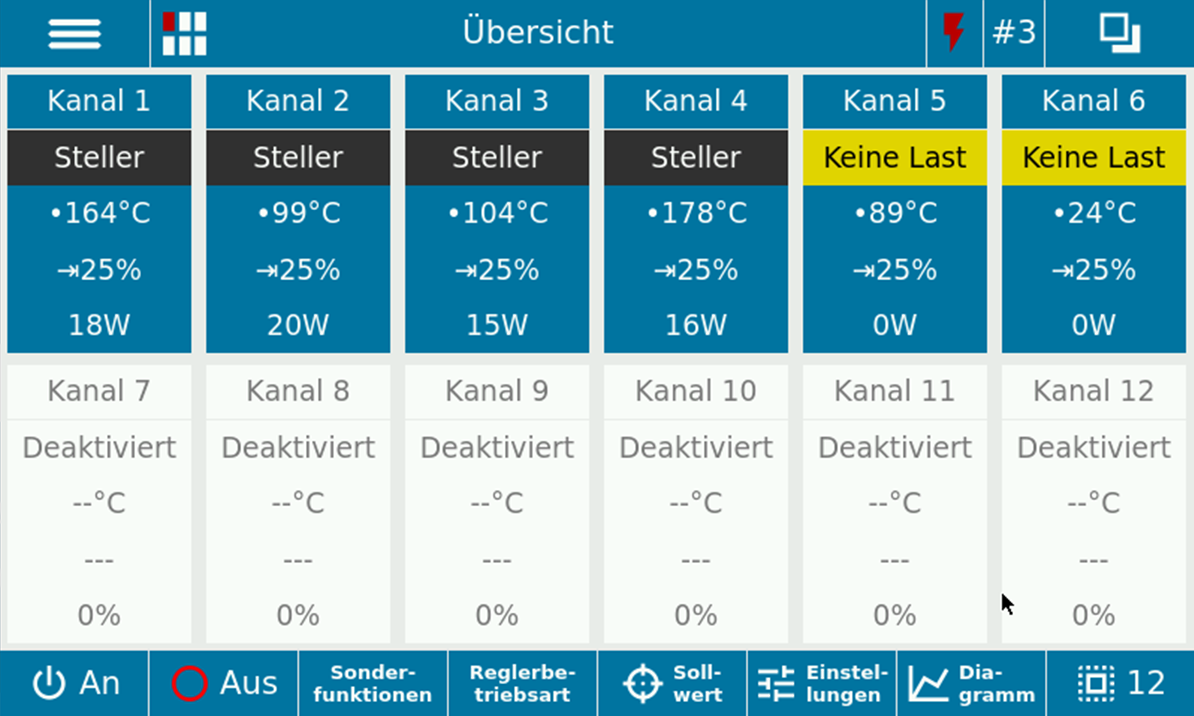
CHANNEL OVERVIEW
The start screen shows an overview of all control zones and allows configuration with just a few clicks.
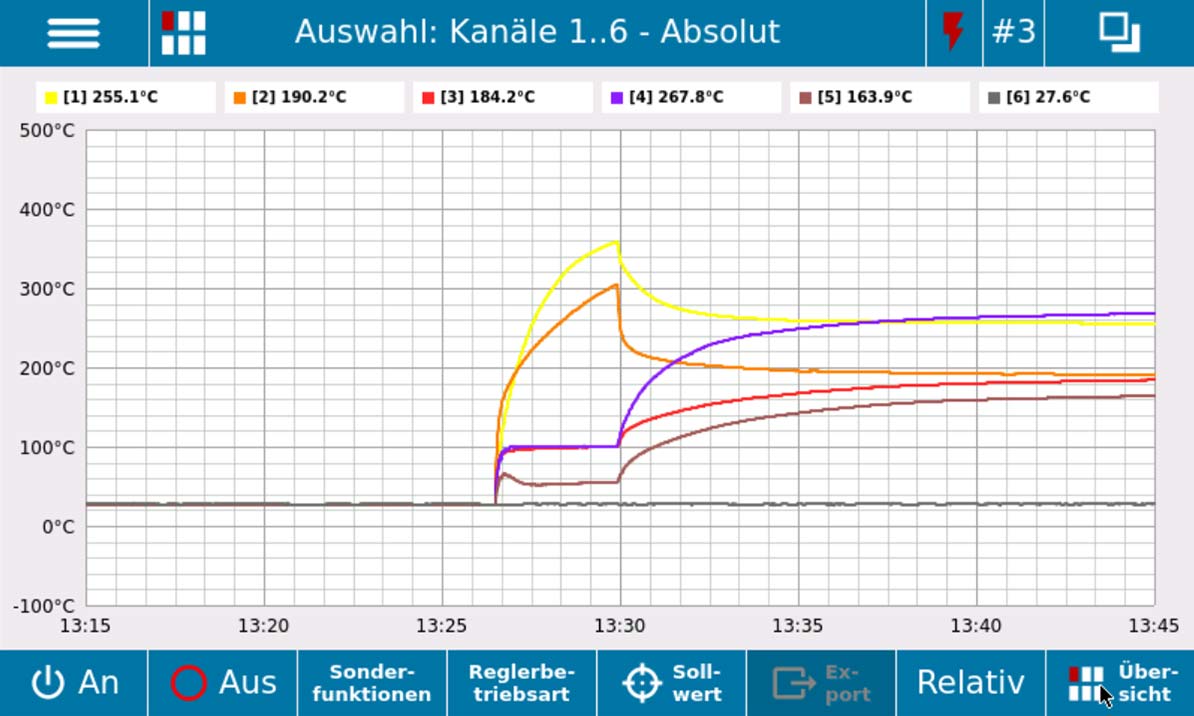
DATA WRITER
Measured temperatures, output level and deviations from the setpoint can be processed and exported in an intuitively customizable diagram.
Specifications
Configuration options
two times 24-pole,
arranged horizontally
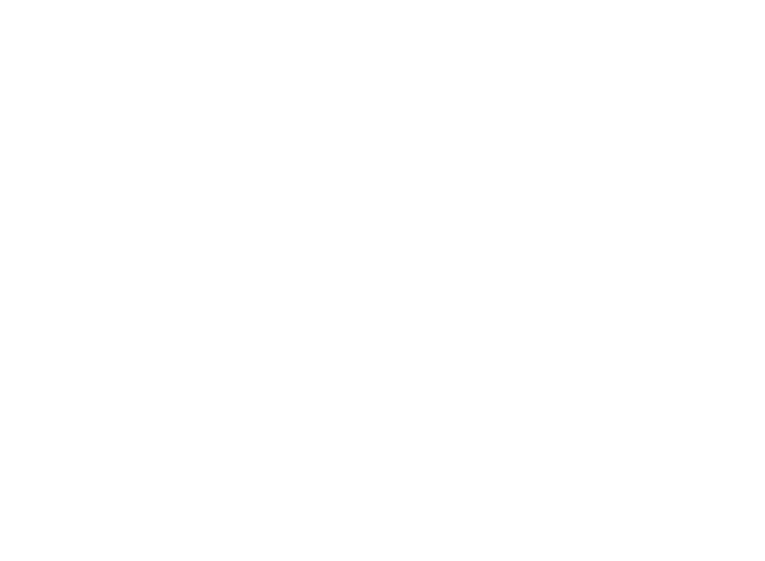
two times 32-pole,
arranged vertically
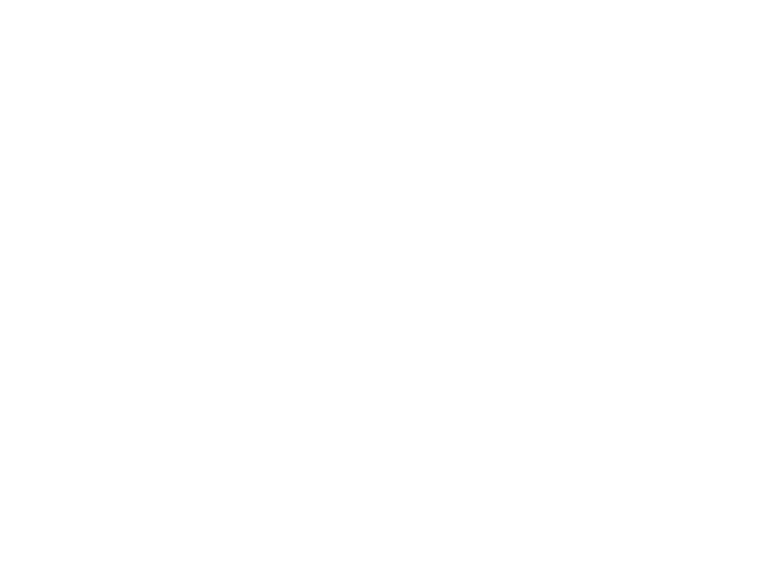
once 32-pole,
once 40-pole
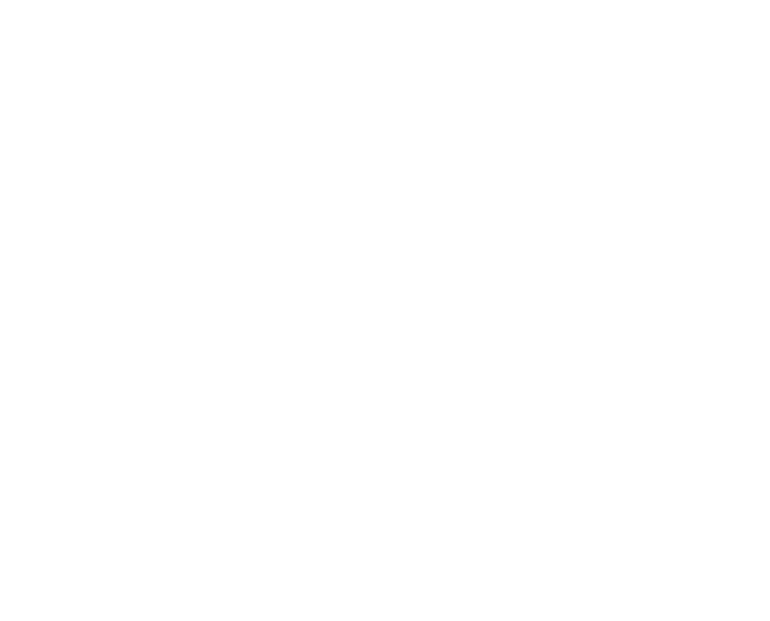
three times 16-pole,
arranged vertically
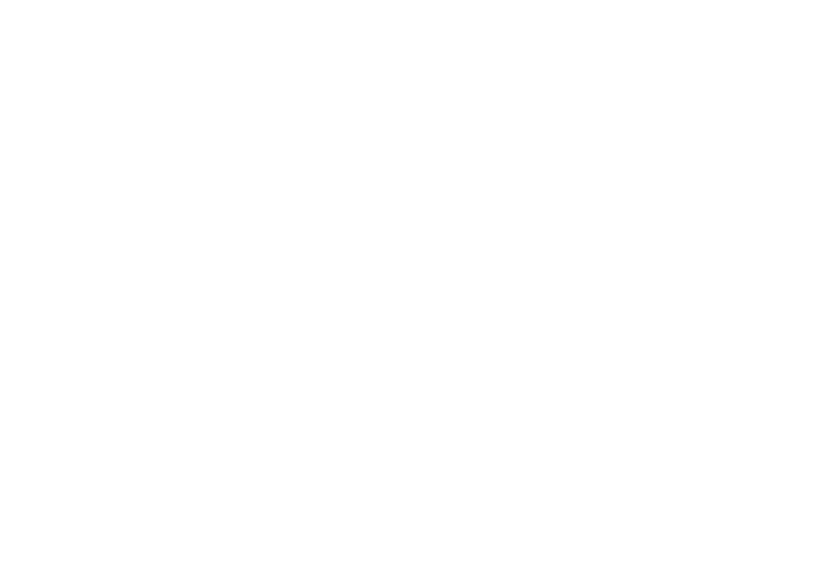
CEE plug 16 A
CEE plug 32 A
CEE plug 63 A
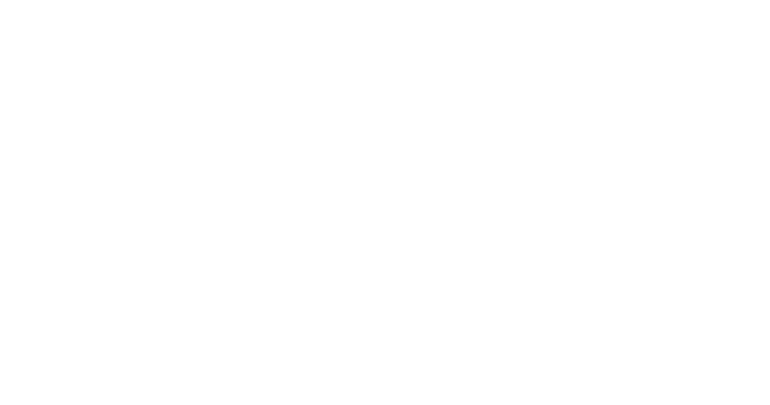
Cable gland M32
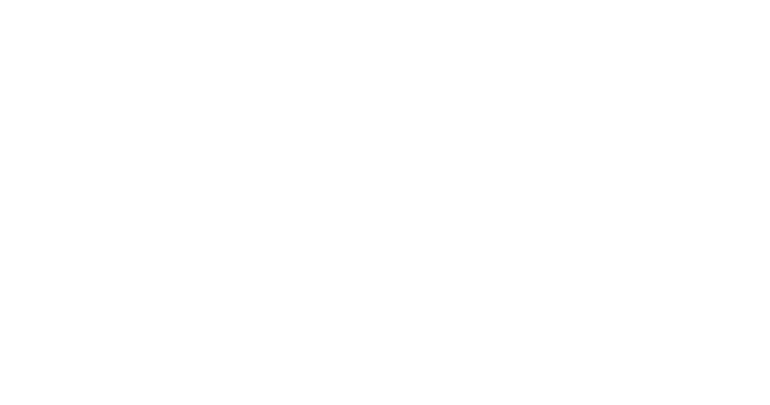
Always up to date!
Customer-oriented user interface with free updates
The user interface of our hot runner controller was developed taking into account many customer suggestions and will be continuously improved and adapted to current requirements in the future. Software updates are generally freely available and can be installed either via an existing network connection or via a USB storage medium.
About us
Production & Support
Intronik GmbH
Am Promigberg 8 | D – 01108 Dresden
Phone +49 (0) 351/88 21-55
Fax +49 (0) 351/88 21-28
Mail info@intronik.de
Web www.intronik.de
Distribution
Kunststofftechnik Nadler GmbH & Co KG
Heinrich-Cotta-Straße 5 | D – 01324 Dresden
Phone +49 (0) 351/26 55 128-0
Fax +49 (0) 351/26 55 128-1
Mail kontakt@kunststofftechnik-nadler.de
Web www.kunststofftechnik-nadler.de