THERMONOM 2G – The most flexible hot runner controller
With the THERMONOM 2G, we offer you an innovative solution for the precise control of hot runners.
The THERMONOM 2G is available in different versions that have been specially developed for different numbers of channels:
Basic model: for applications with 6 / 12 channels | Medium variants: for 18 / 24, 30 / 36 and 42 / 48 channels | Largest model: 54 / 60 channels
Regardless of the number of channels you have, you get a compact and powerful device that guarantees maximum precision and reliability.
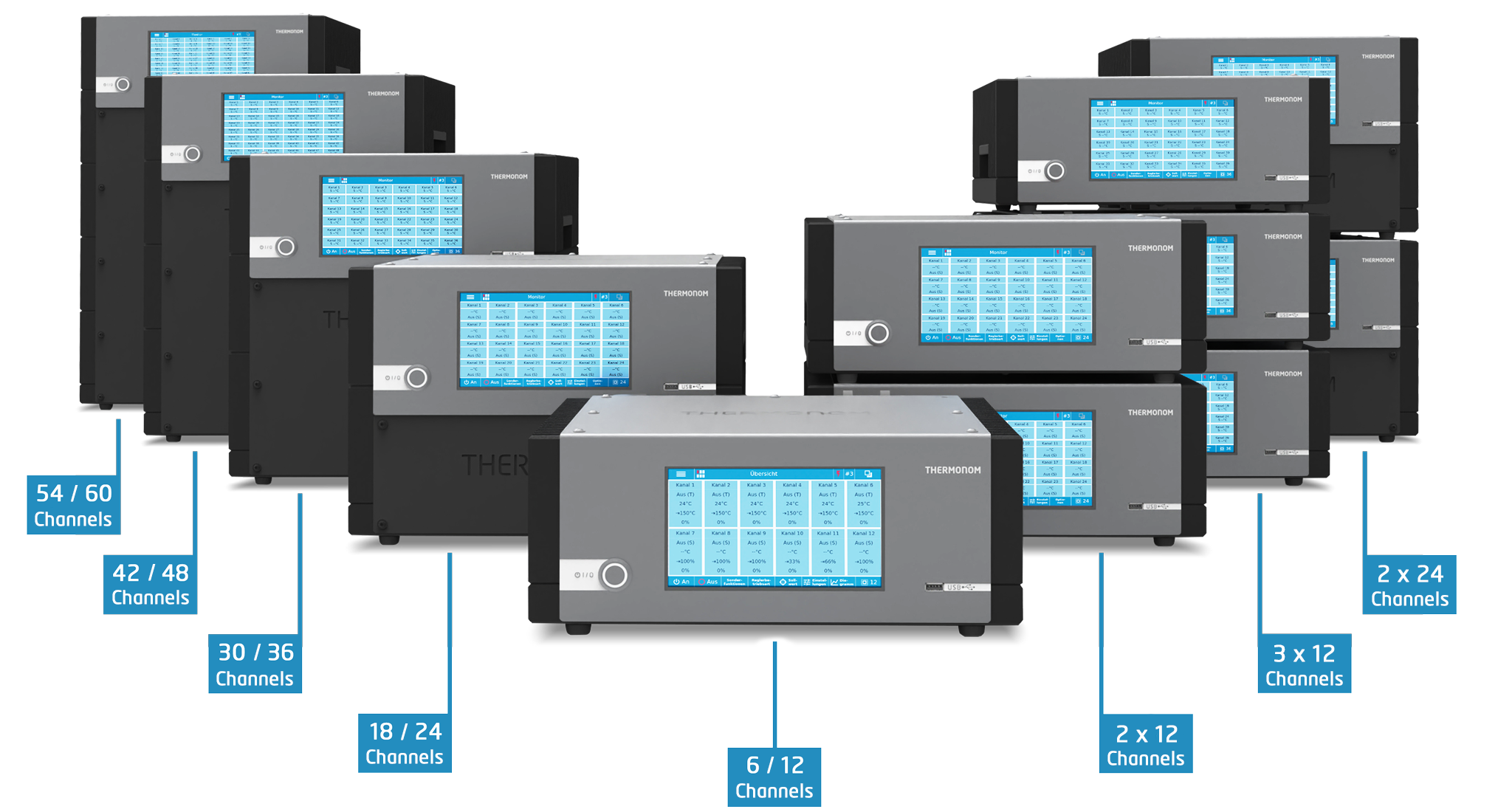
Compact, powerful and ready to go!

Flexibly scalable, without compromise!
Flexible, modular and perfectly tailored to your requirements
Do you need more than 60 channels? No problem! Thanks to the Coupling function several THERMONOME units can be connected together to form a common control unit. This allows up to 192 channels ideal for large and complex applications.
All versions of the THERMONOM are fully compatible with each other, regardless of size or generation. You can even seamlessly combine the first generation THERMONOM with the new THERMONOM 2G
This makes integration into existing systems simple and cost-efficient.
Clear & intuitive operation
Easy-to-understand operating functions for effortless handling without extensive training
Guided Service
The Guided Service uses QR codes on the hot runner controller to provide quick access to a media library with technical videos that explain installation, operation and maintenance step by step.
Interfaces & connectivity
The THERMONOM offers versatile interfaces for easy integration into your injection moulding environment – whether for machine connection, for coupling with other controllers or for external control via LAN, WLAN, CAN, RS232, RS485 or customer-specific IO signals.
Extensive monitoring & diagnostic options
Detect problems early, minimize downtime, maximize uptime
Clear & intuitive operation
Easy-to-understand operating functions for effortless handling without extensive training
Guided Service
The Guided Service uses QR codes on the hot runner controller to provide quick access to a media library with technical videos that explain installation, operation and maintenance step by step.
Interfaces & connectivity
The THERMONOM offers versatile interfaces for easy integration into your injection moulding environment – whether for machine connection, for coupling with other controllers or for external control via LAN, WLAN, CAN, RS232, RS485 or customer-specific IO signals.
Extensive monitoring & diagnostic options
Detect problems early, minimize downtime, maximize uptime
Easy maintenance in no time at all
Thanks to independently replaceable controller electronics modules, maintenance and repairs are child’s play.
Simply unplug the old module and plug in the new one – quickly and easily.
The 6-channel module is available as a spare part for easy replacement.
*The triacand fuse are installed directly on the module as individual spare parts and can be replaced quickly and easily if necessary.
Easy maintenance in no time at all
Thanks to independently replaceable controller electronics modules, maintenance and repairs are child’s play.
Simply unplug the old module and plug in the new one – quickly and easily.
The 6-channel module is available as a spare part for easy replacement.
*The triacand fuse are installed directly on the module as individual spare parts and can be replaced quickly and easily if necessary.
Characteristics of the THERMONOM
SHORT-CIRCUIT PROOF &
REVERSE POLARITY PROTECTED
- Detection of incorrectly connected temperature sensors
- Software backup
QUICK SETUP
- PID controller with automatic adaptation
- Wizard – quick configuration when changing tools
- Diagnostic function for toolmakers and setters
FANLESS DESIGN
- Fanless design with convective cooling of the power electronics
- Fan can be retrofitted for high-power applications
EXTREMELY COMPACT SIZE
- Robust housing construction, anodized aluminium
- The footprint is barely larger than an A4 page,
the height varies depending on the number of channels
MULTIPLE OPERATING PATHS
- Control directly on the device via integrated touch display
- Flexible operation via notebook or tablet
- Seamless control via the injection molding machine (interface connection)
CONFIGURABLE CONNECTOR & PIN ASSIGNMENT
- Flexible adaptation to the number of channels and requirements thanks to configurable connector and pin assignment
Characteristics of the THERMONOM
SHORT-CIRCUIT PROOF &
REVERSE POLARITY PROTECTED
- Detection of incorrectly connected temperature sensors
- Software backup
QUICK
SETUP
- PID controller with automatic adaptation
- Wizard – quick configuration when changing tools
- Diagnostic function for toolmakers and setters
FANLESS DESIGN
- Fanless design with convective cooling of the power electronics
- Fan can be retrofitted for high-power applications
EXTREMELY COMPACT SIZE
- Robust housing construction, anodized aluminium
- The footprint is barely larger than an A4 page,
the height varies depending on the number of channels
MULTIPLE OPERATING PATHS
- Control directly on the device via integrated touch display
- Flexible operation via notebook or tablet
- Seamless control via the injection molding machine (interface connection)
CONFIGURABLE CONNECTOR & PIN ASSIGNMENT
- Flexible adaptation to the number of channels and requirements thanks to configurable connector and pin assignment
- Simple and precise wiring of the hot runner controller possible
Intuitive operation at all levels
Our hot runner controller impresses with its user-friendly and intuitive operation!
Thanks to the integrated touch display, you can control all functions directly on the device with just a few taps. Alternatively, the cloud connection offers you full flexibility: you can access the controller functions anytime and anywhere via notebook or tablet. In addition, the seamless interface connection enables direct control via the injection molding machine – for maximum efficiency and optimum integration into your production processes.
Experience simple, flexible and future-proof operation at the highest level!
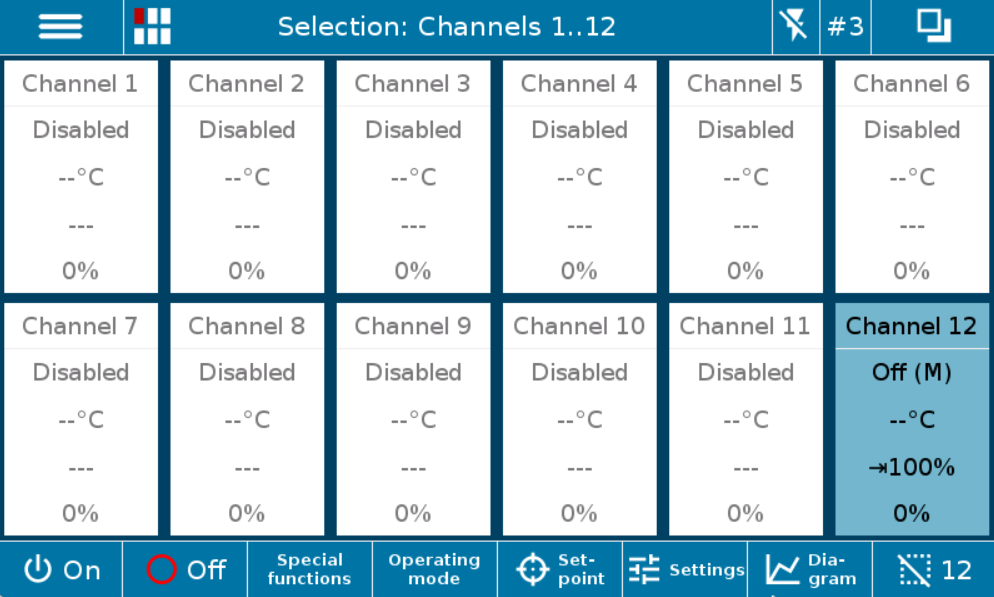
CHANNEL OVERVIEW
In the main view, all zones are displayed together with the associated process values. The display of the zones can be customized with just a few clicks so that it is individually tailored to each application.
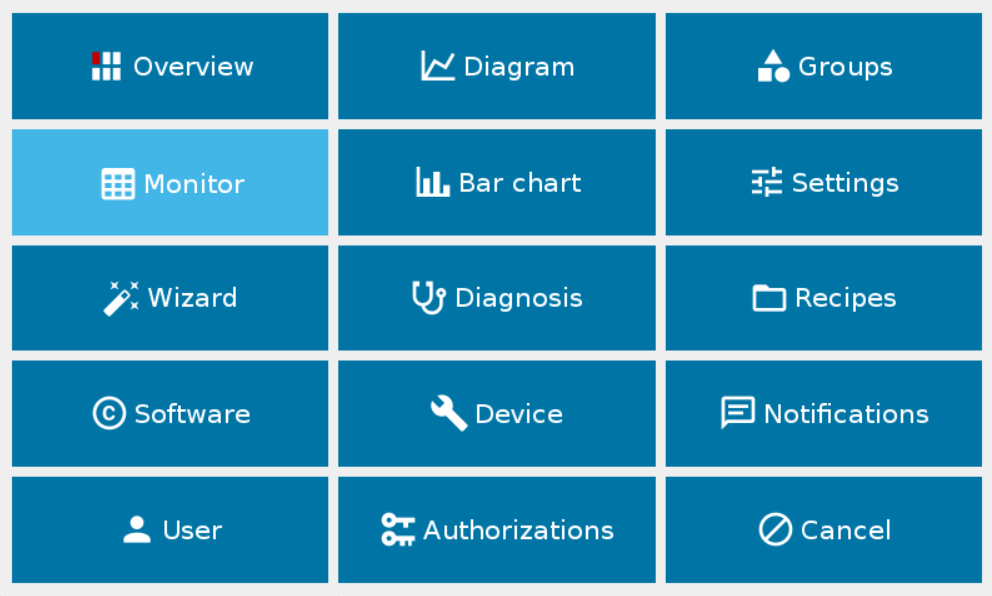
MAIN MENU
All functions relating to the views of the channels and the control are clearly arranged in the navigation menu and easily accessible. Important settings of the hot runner controller can be reliably protected against unintentional changes by a user control.
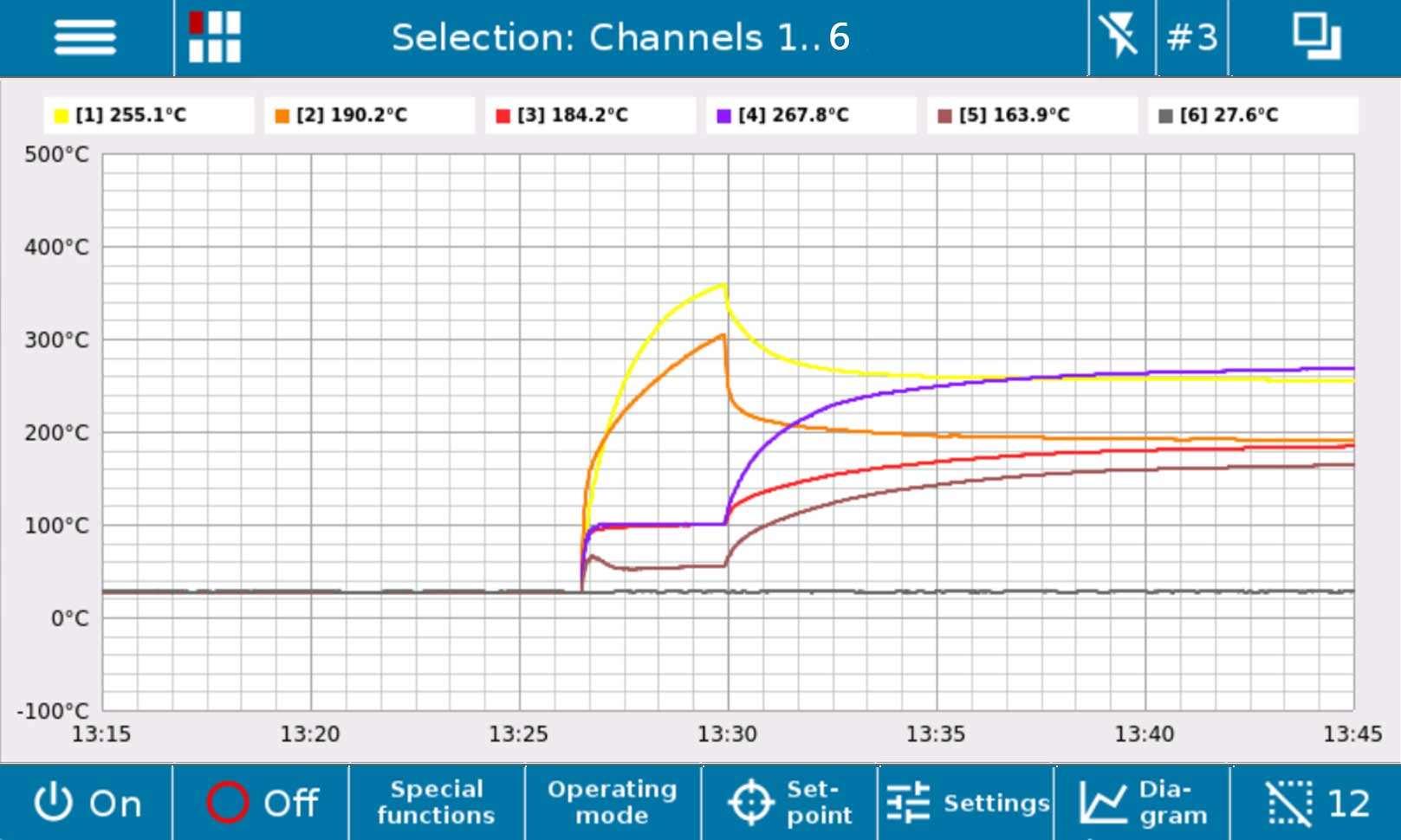
DATA WRITER
The curve recorder makes it easy to analyze the zones by displaying the actual value, setpoint and output level in a customizable diagram. Temperature curves can be tracked live, zoomed, paused and exported for evaluation.
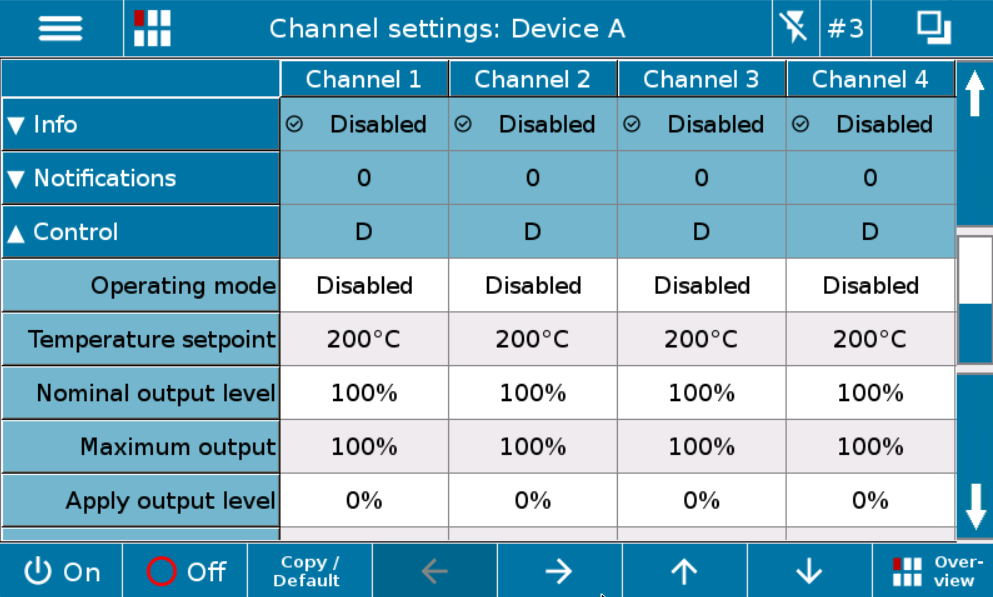
CHANNEL SETTINGS
All current values and statuses are displayed in the channel settings, and setpoints, operating modes, warning limits, control parameters, temperature sensors, special functions, current measurements and error behavior can be set.
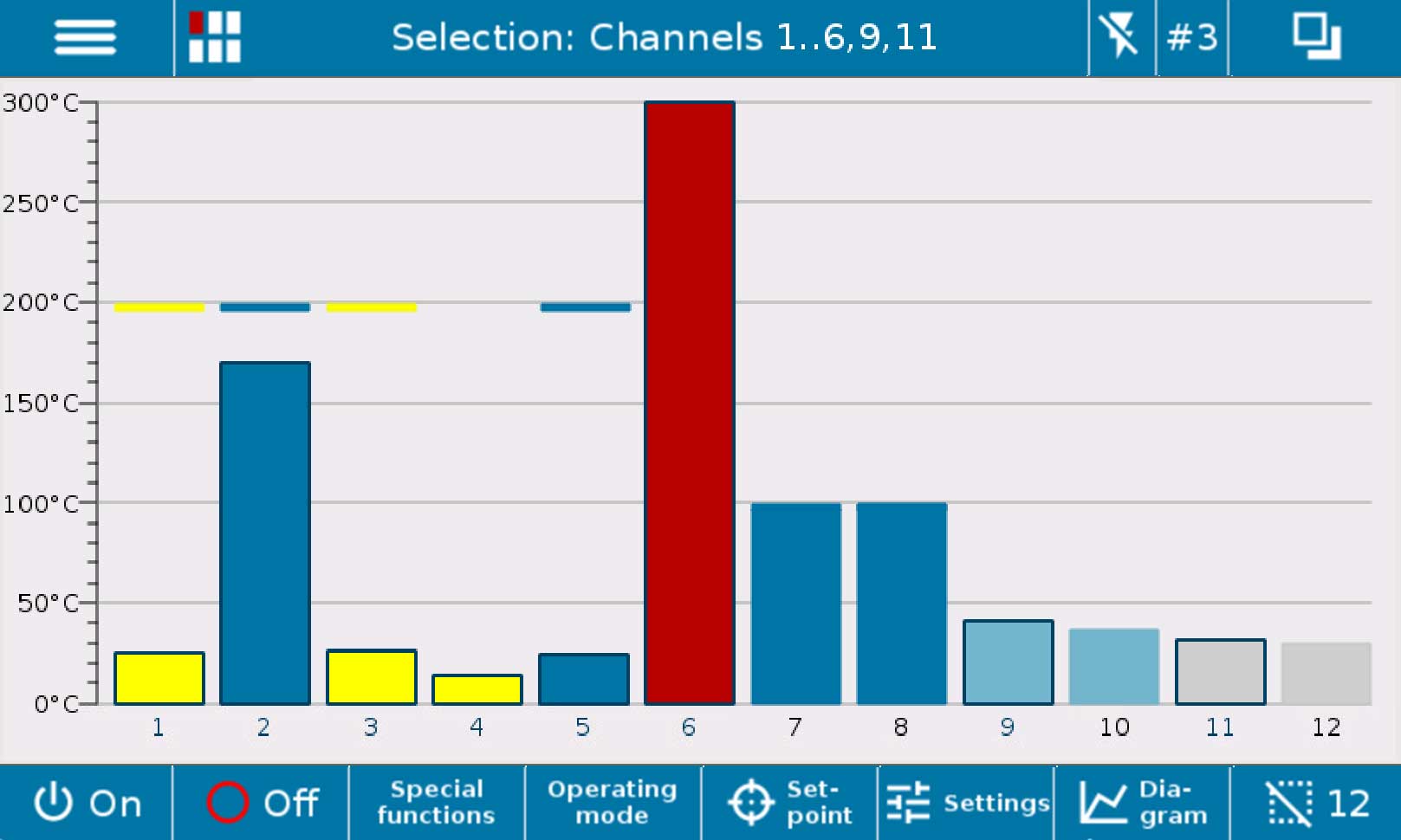
BALKET DIAGRAM
The bar chart shows the status and temperatures of the channels in color, allowing you to select and control individual channels and visually identify their actual and target temperatures.
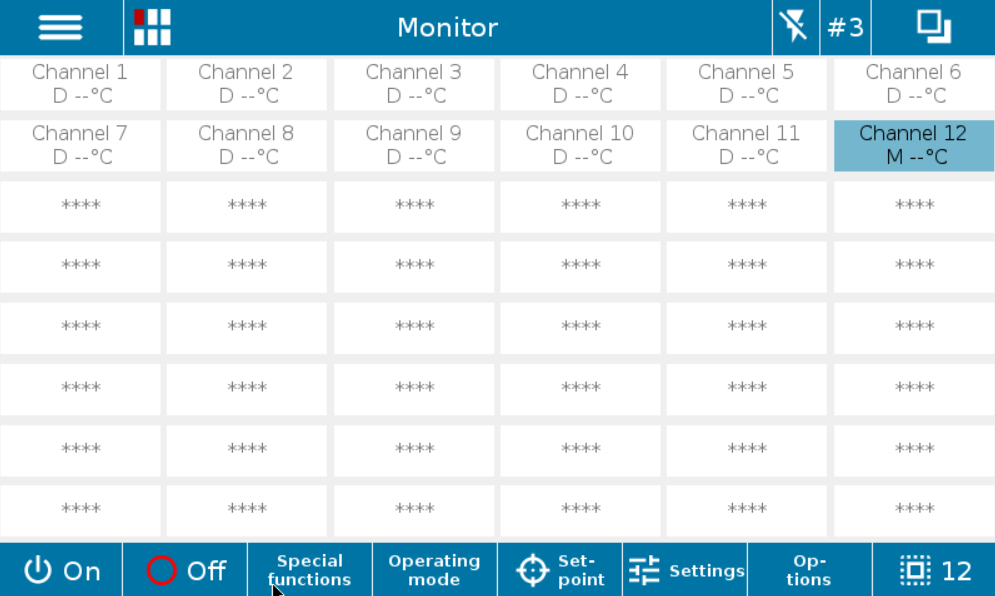
MONITOR
The “Coupling” function in the “Device settings” allows you to combine several THERMONOM hot runner controllers into one unit. Monitor views with 24, 36, 48, 60 or 96 channels are available to provide a quick overview of all channels.
Customer-oriented user interface with free updates
The user interface of the THERMONOMS was developed taking into account many customer suggestions and will be continuously improved and adapted to current requirements in the future. Software updates are generally freely available and can be installed either via an existing network connection or via a USB storage medium.
Intuitive operation at all levels
Our hot runner controller impresses with its user-friendly and intuitive operation!
Thanks to the integrated touch display, you can control all functions directly on the device with just a few taps. Alternatively, the cloud connection offers you full flexibility: you can access the controller functions anytime and anywhere via notebook or tablet. In addition, the seamless interface connection enables direct control via the injection molding machine – for maximum efficiency and optimum integration into your production processes.
Experience simple, flexible and future-proof operation at the highest level!
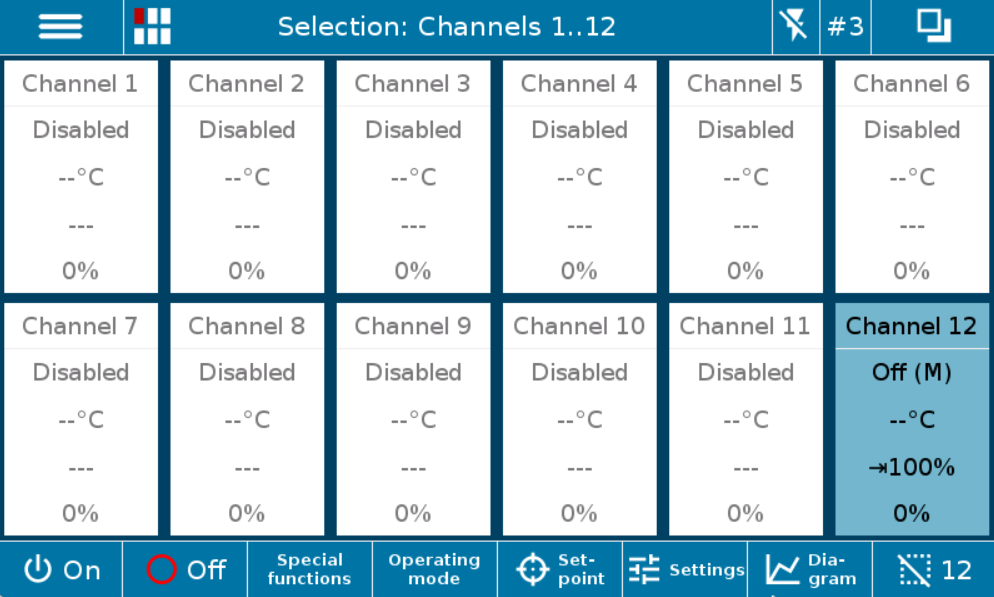
CHANNEL OVERVIEW
In the main view, all zones are displayed together with the associated process values. The display of the zones can be customized with just a few clicks so that it is individually tailored to each application.
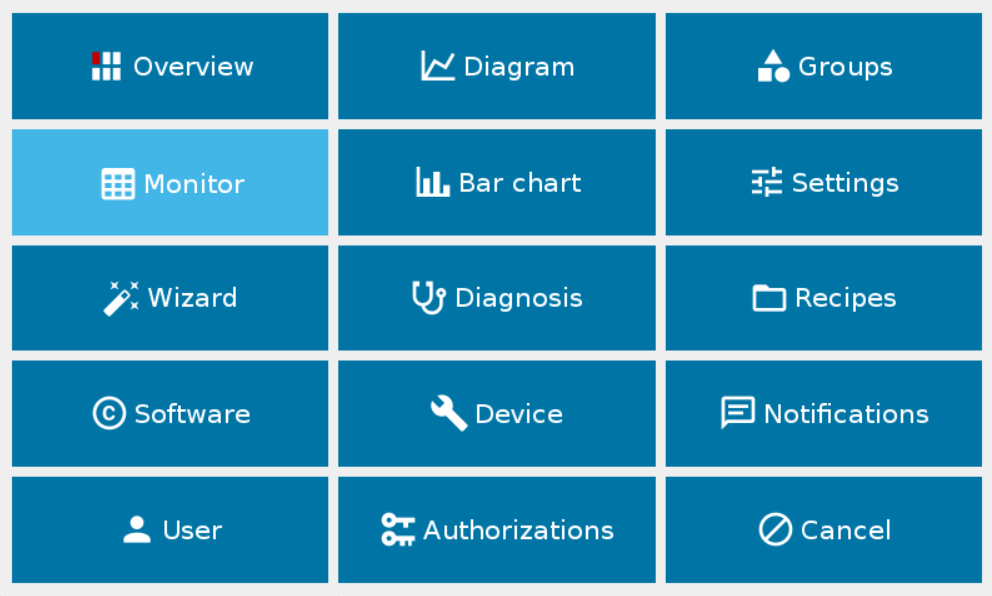
MAIN MENU
All functions relating to the views of the channels and the control are clearly arranged in the navigation menu and easily accessible. Important settings of the hot runner controller can be reliably protected against unintentional changes by a user control.
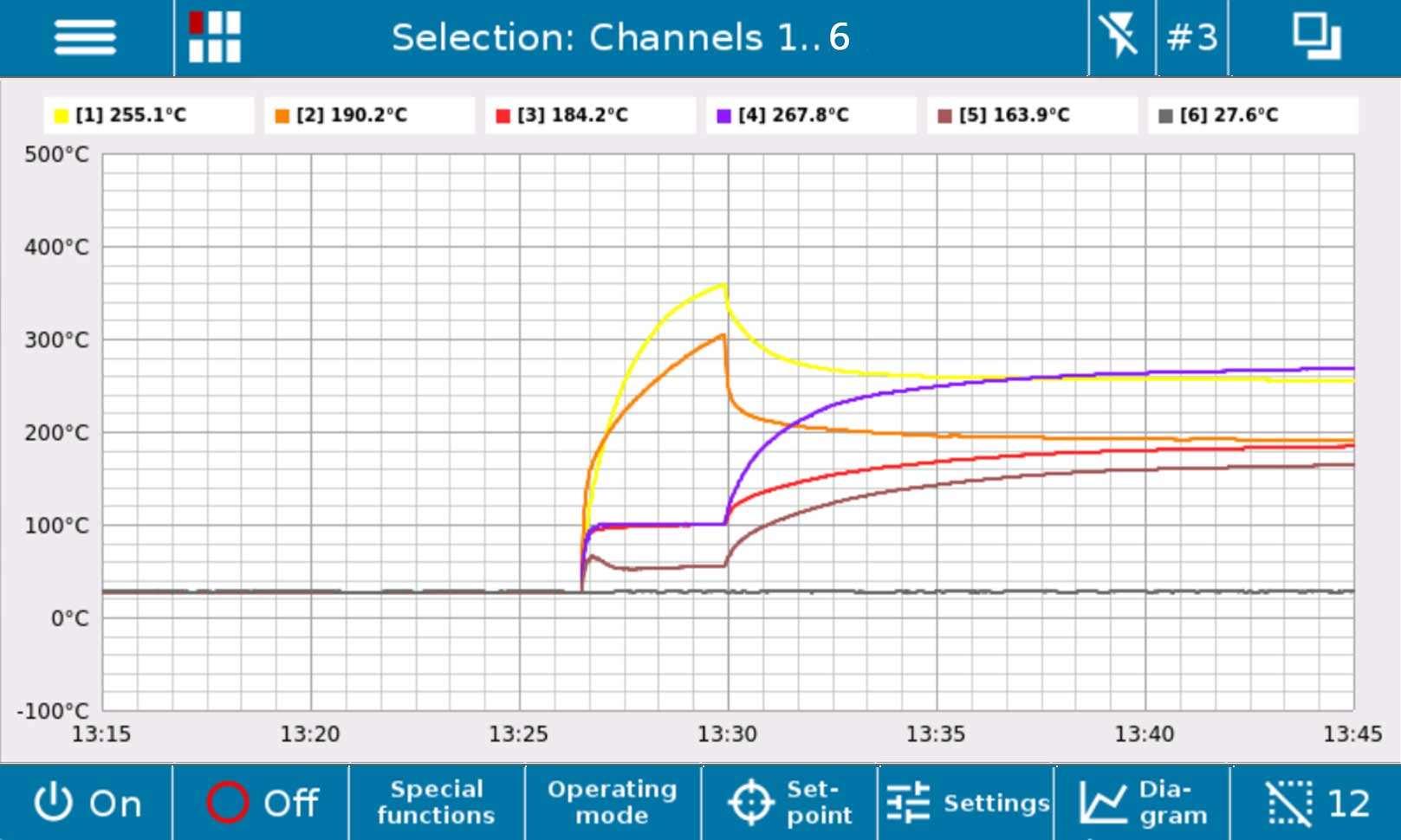
DATA WRITER
The curve recorder makes it easy to analyze the zones by displaying the actual value, setpoint and output level in a customizable diagram. Temperature curves can be tracked live, zoomed, paused and exported for evaluation.
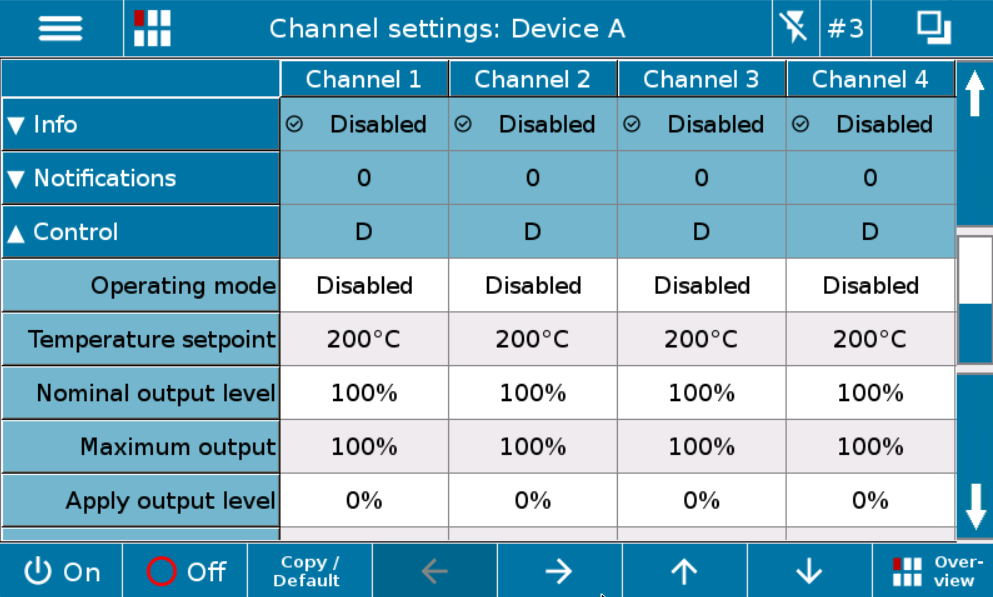
CHANNEL SETTINGS
All current values and statuses are displayed in the channel settings, and setpoints, operating modes, warning limits, control parameters, temperature sensors, special functions, current measurements and error behavior can be set.
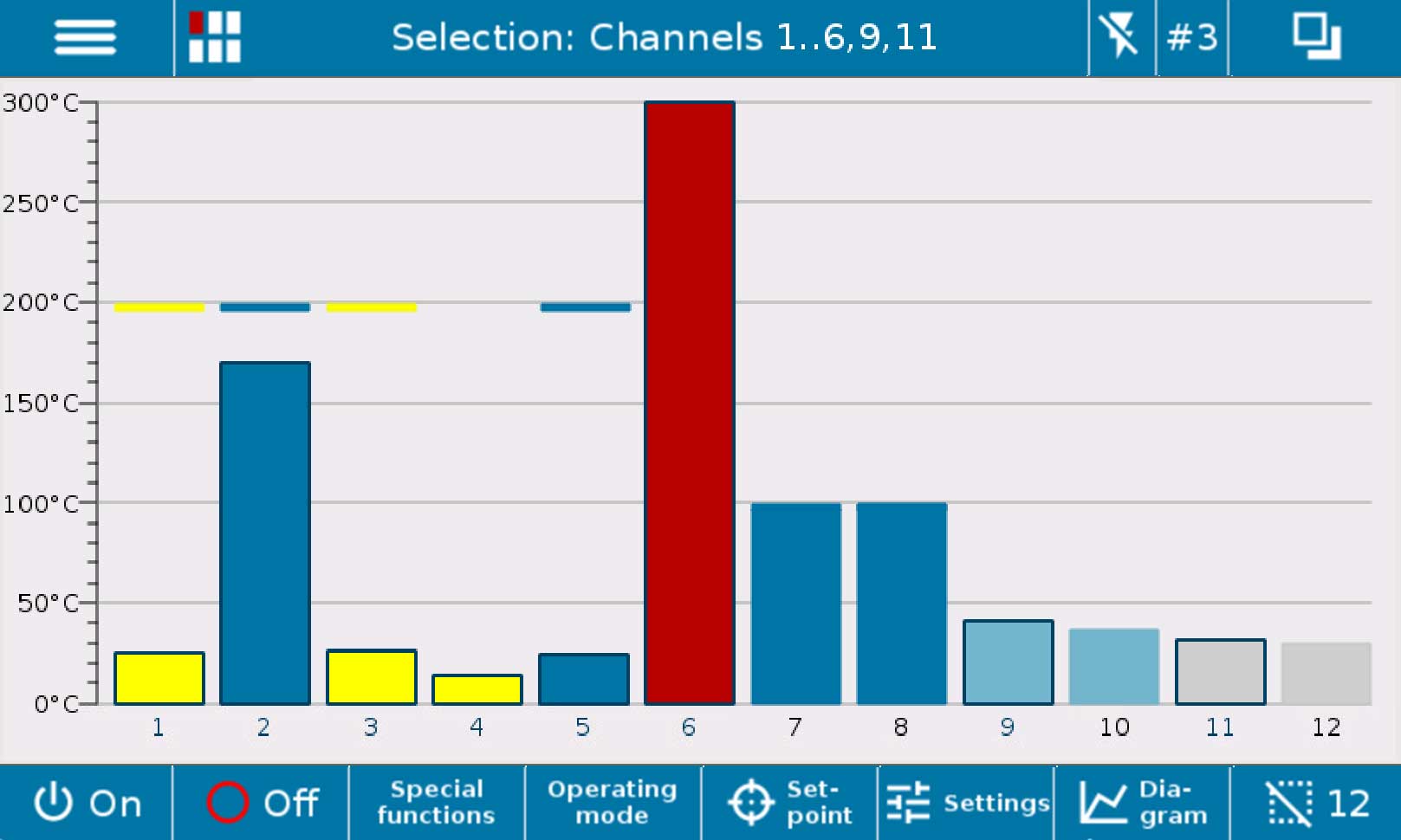
BALKET DIAGRAM
The bar chart shows the status and temperatures of the channels in color, allowing you to select and control individual channels and visually identify their actual and target temperatures.
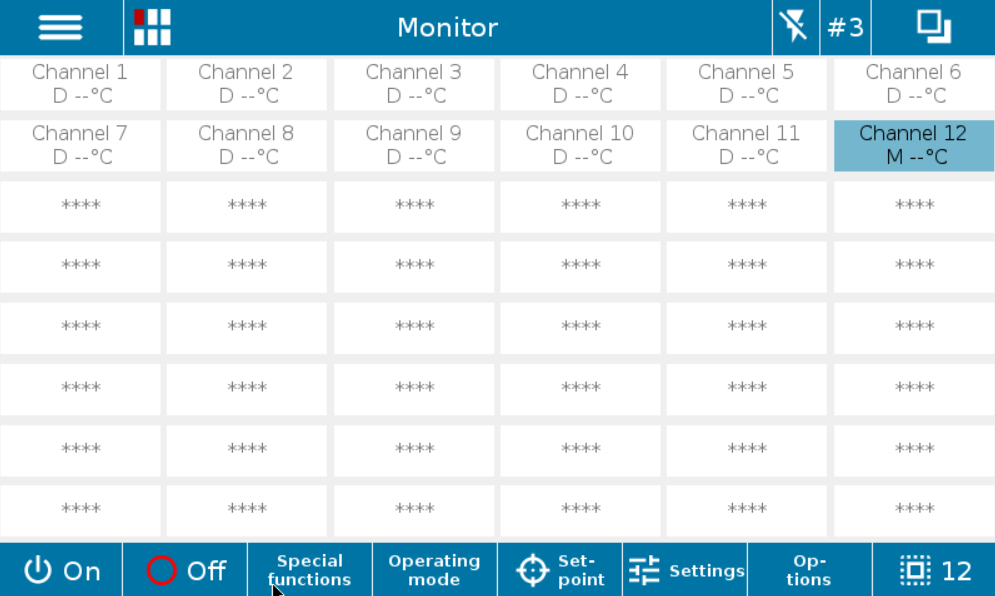
MONITOR
The “Coupling” function in the “Device settings” allows you to combine several THERMONOM hot runner controllers into one unit. Monitor views with 24, 36, 48, 60 or 96 channels are available to provide a quick overview of all channels.
Customer-oriented user interface with free updates
The user interface of the THERMONOMS was developed taking into account many customer suggestions and will be continuously improved and adapted to current requirements in the future. Software updates are generally freely available and can be installed either via an existing network connection or via a USB storage medium.
All functions at a glance
Plug variety
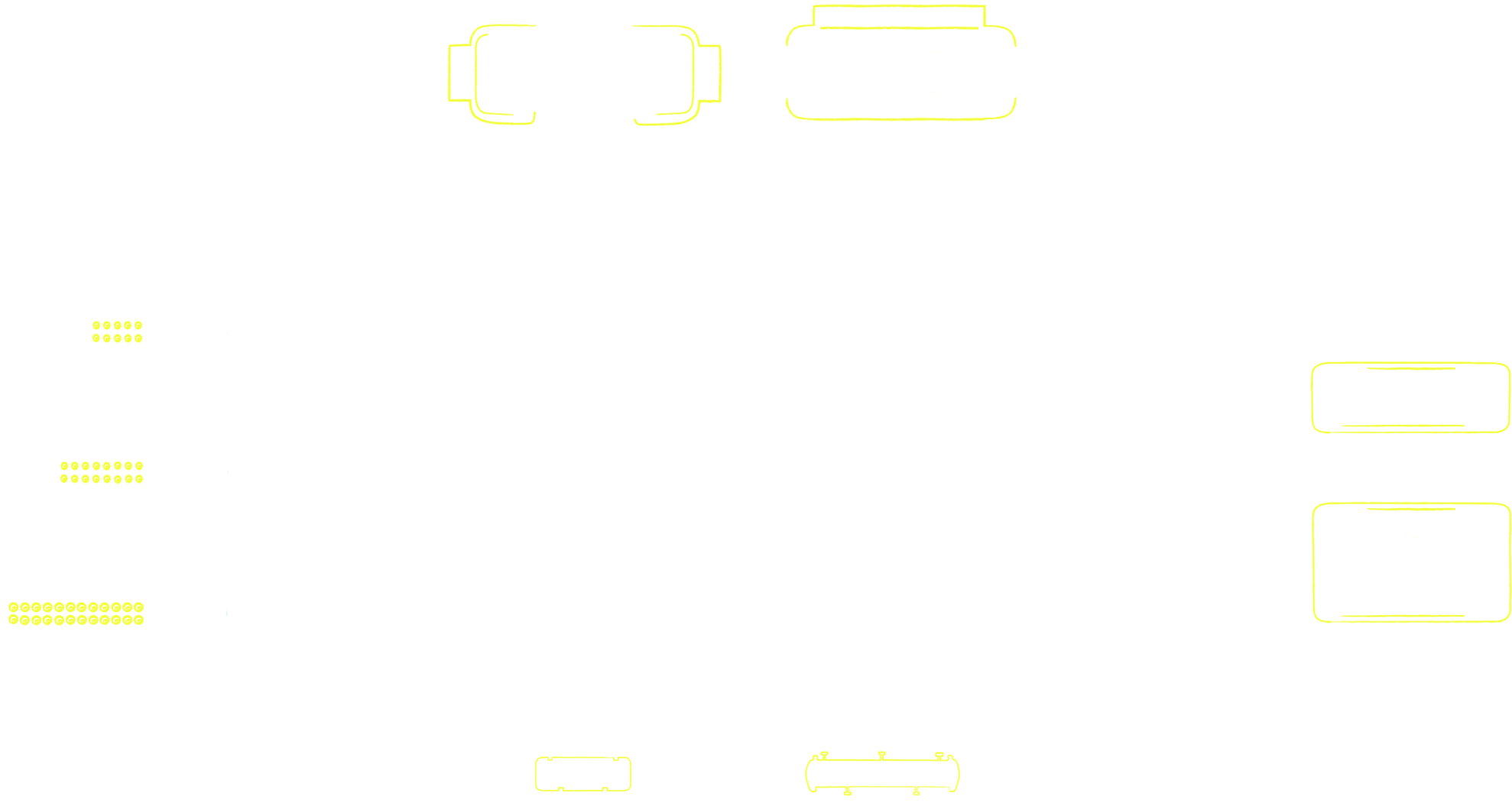
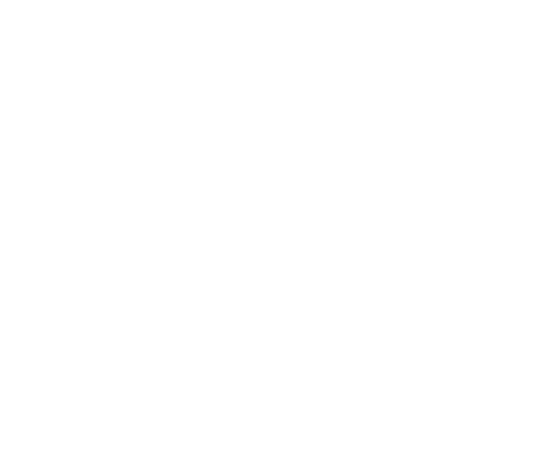
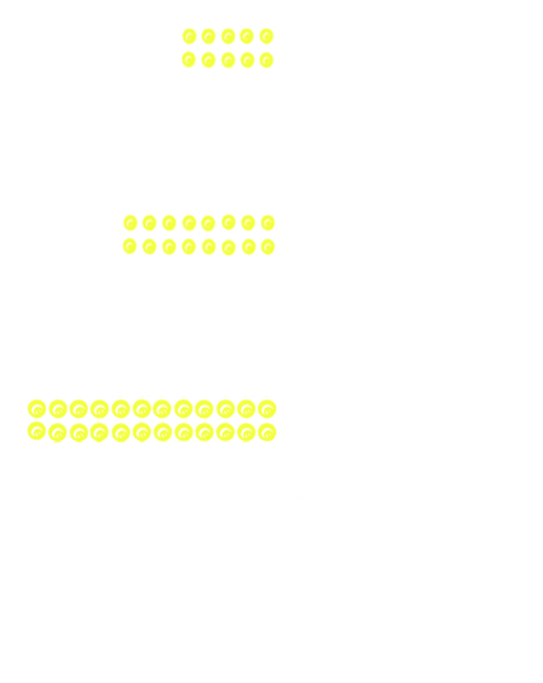
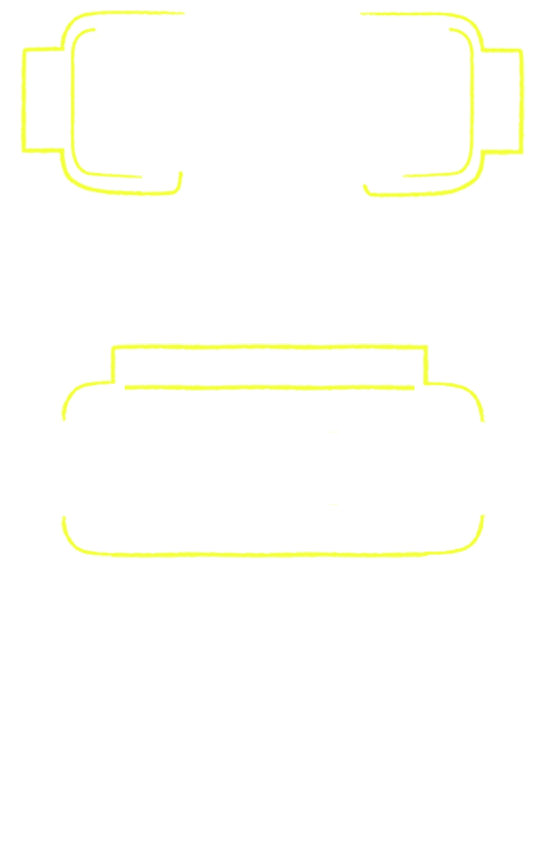
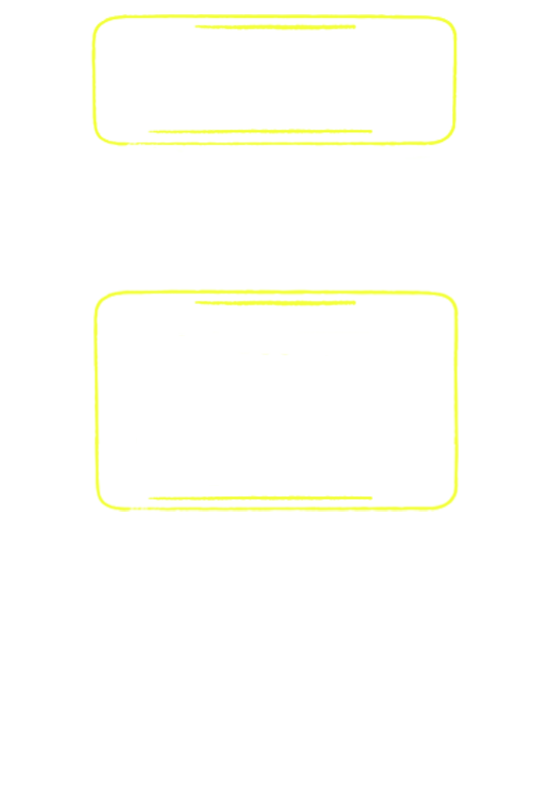
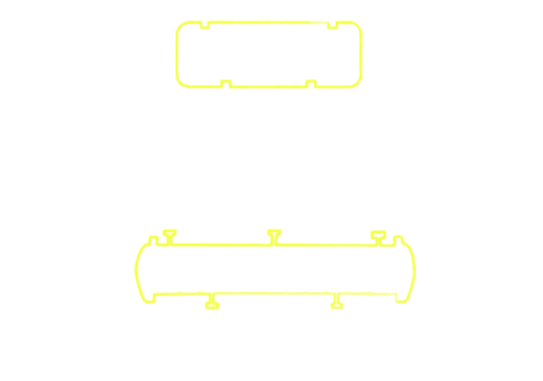
CEE plug 16 A
CEE plug 32 A
CEE plug 63 A
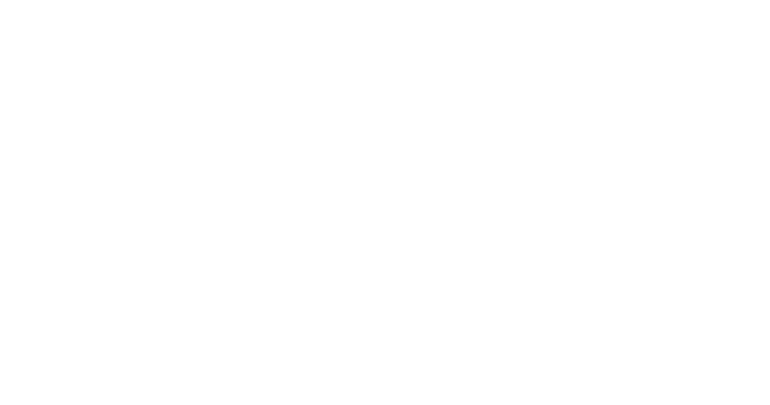
Cable gland M32
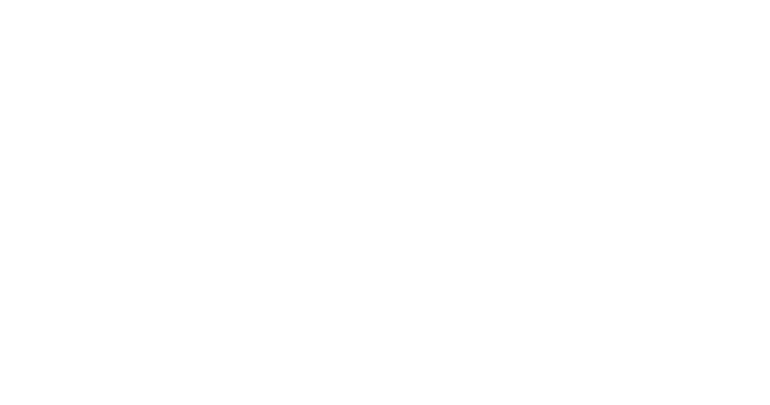
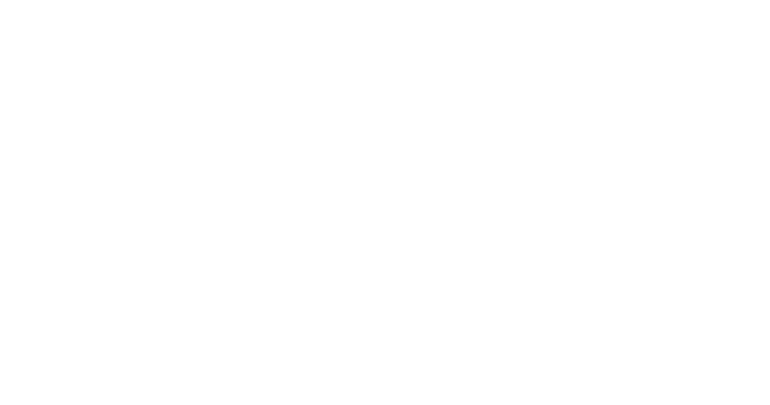
CEE plug 16 A
CEE plug 32 A
CEE plug 63 A
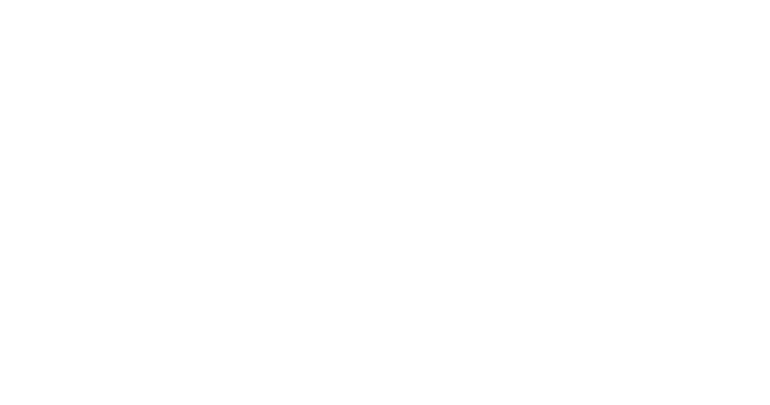
Cable gland M32
Configure now and request a personalized quote directly!
With our visual online configurator, you can easily put together your own hot runner controller:
Select the number of channels, CEE connector, mold connector and pin assignment – and add features such as WLAN, RFID or OPC UA if required. You can see your device exactly as you need it in real time.
Dimensions, performance & details
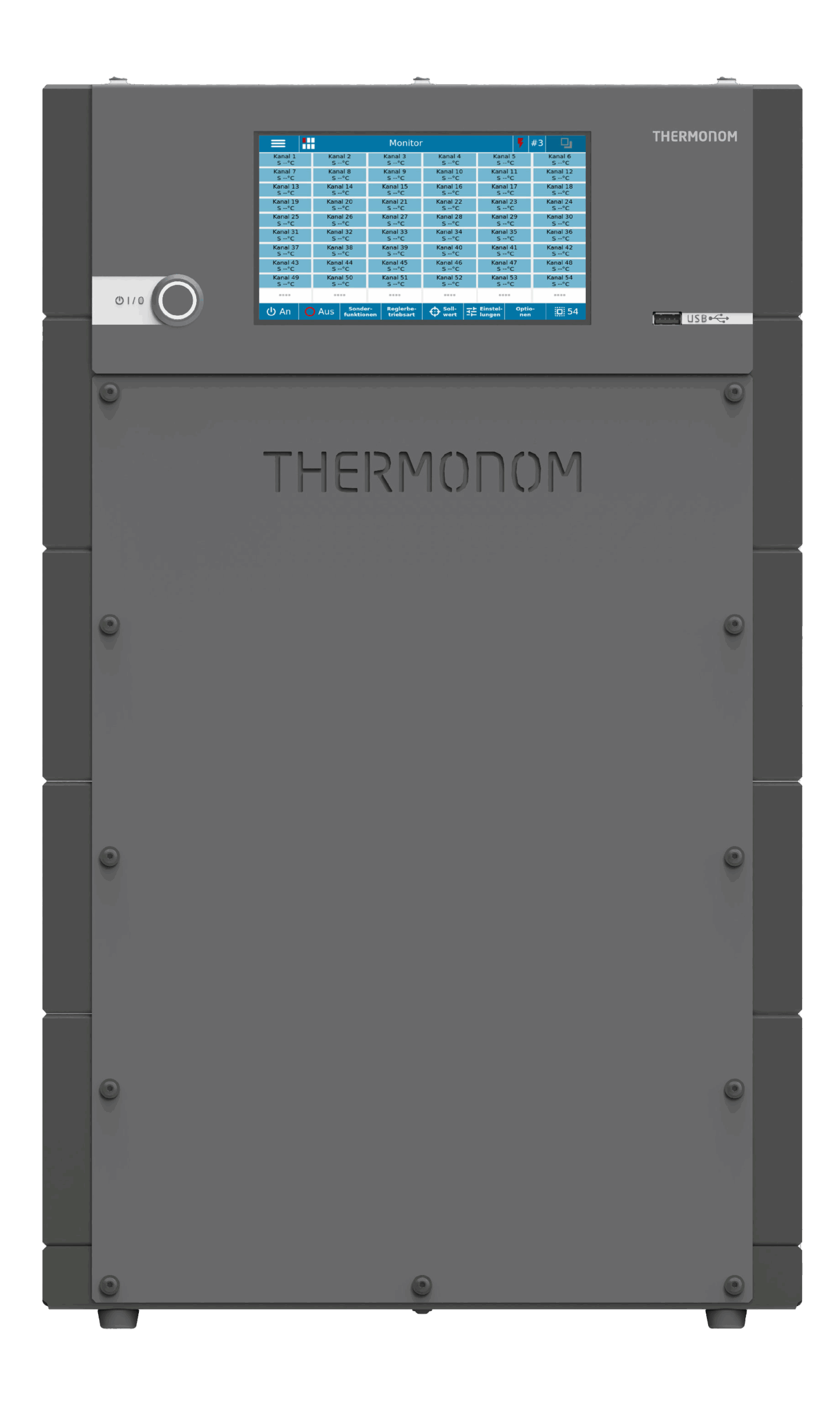
54 / 60 channels
(W x H x D)
360 X 593 X 307 mm
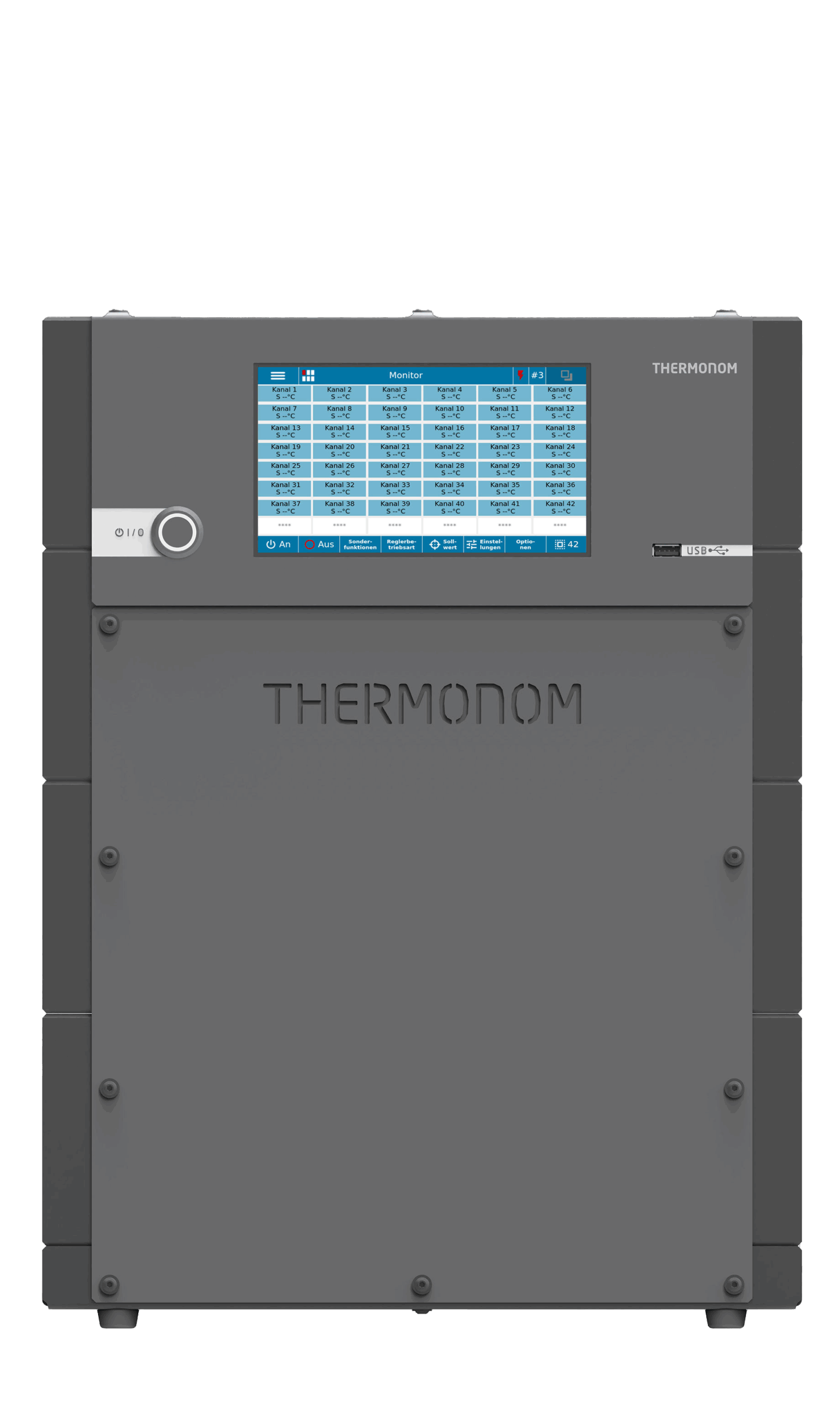
42 / 48 channels
(W x H x D)
360 X 483 X 307 mm
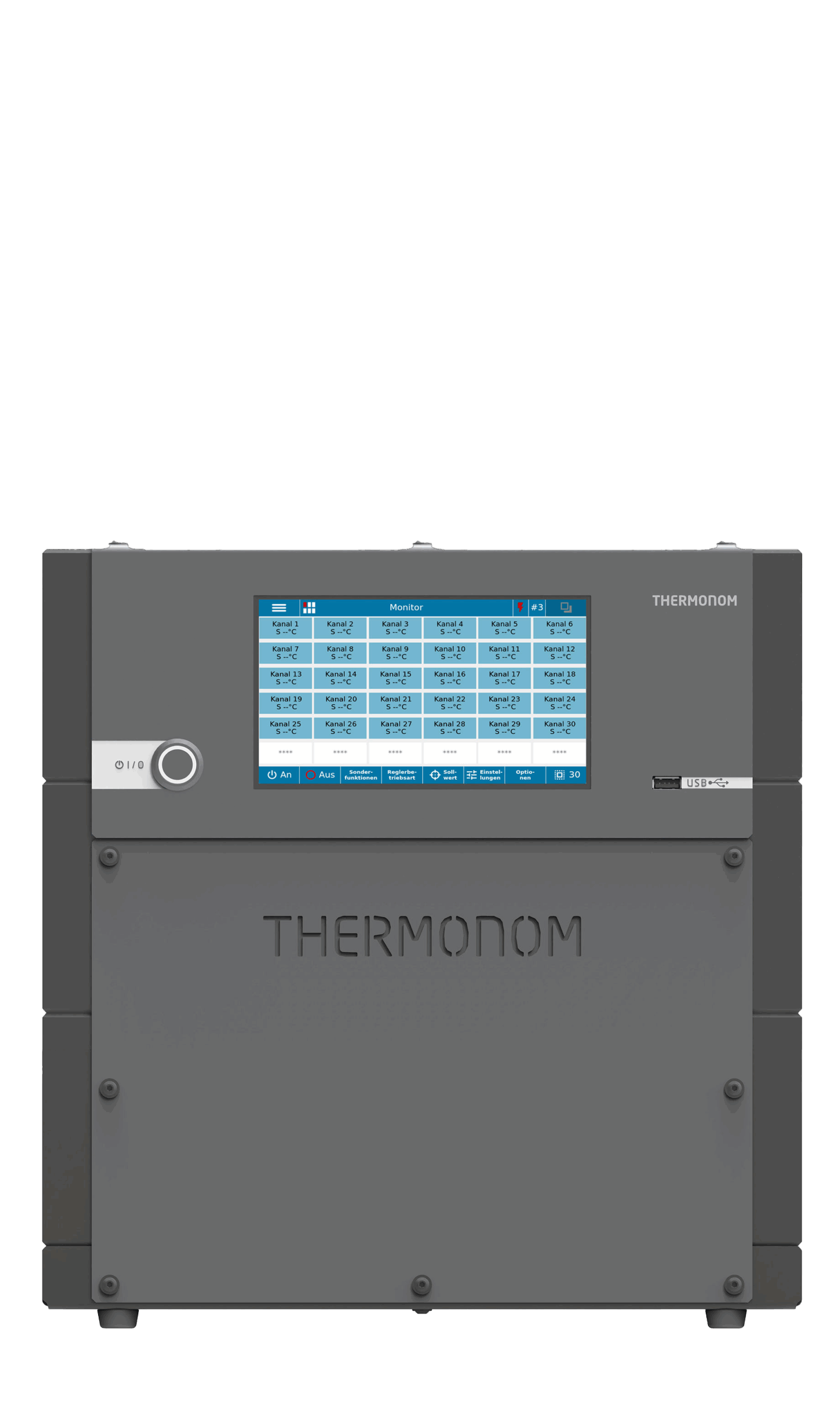
30 / 36 channels
(W x H x D)
360 X 373 X 307 mm
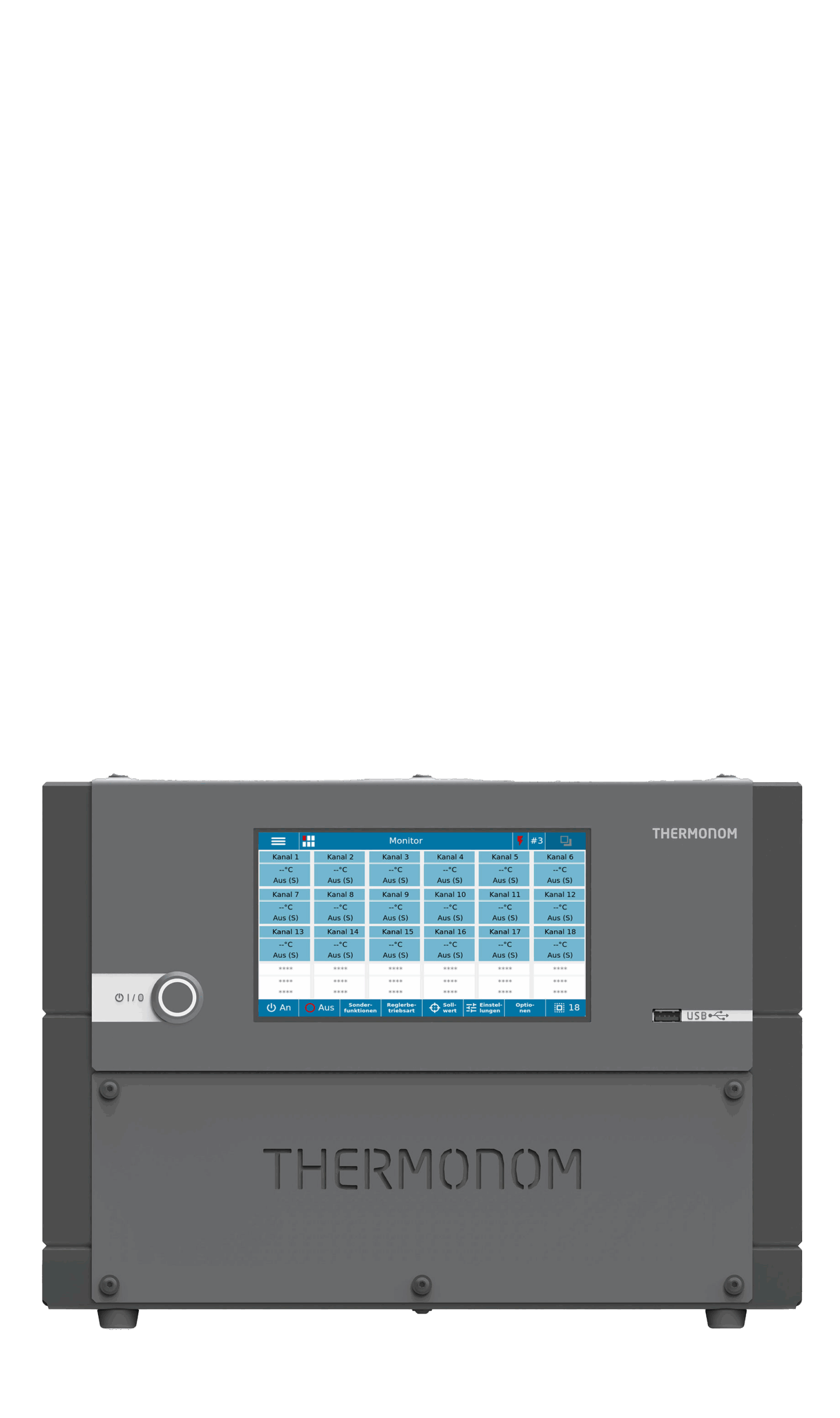
18 / 24 channels
(W x H x D)
360 X 263 X 307 mm
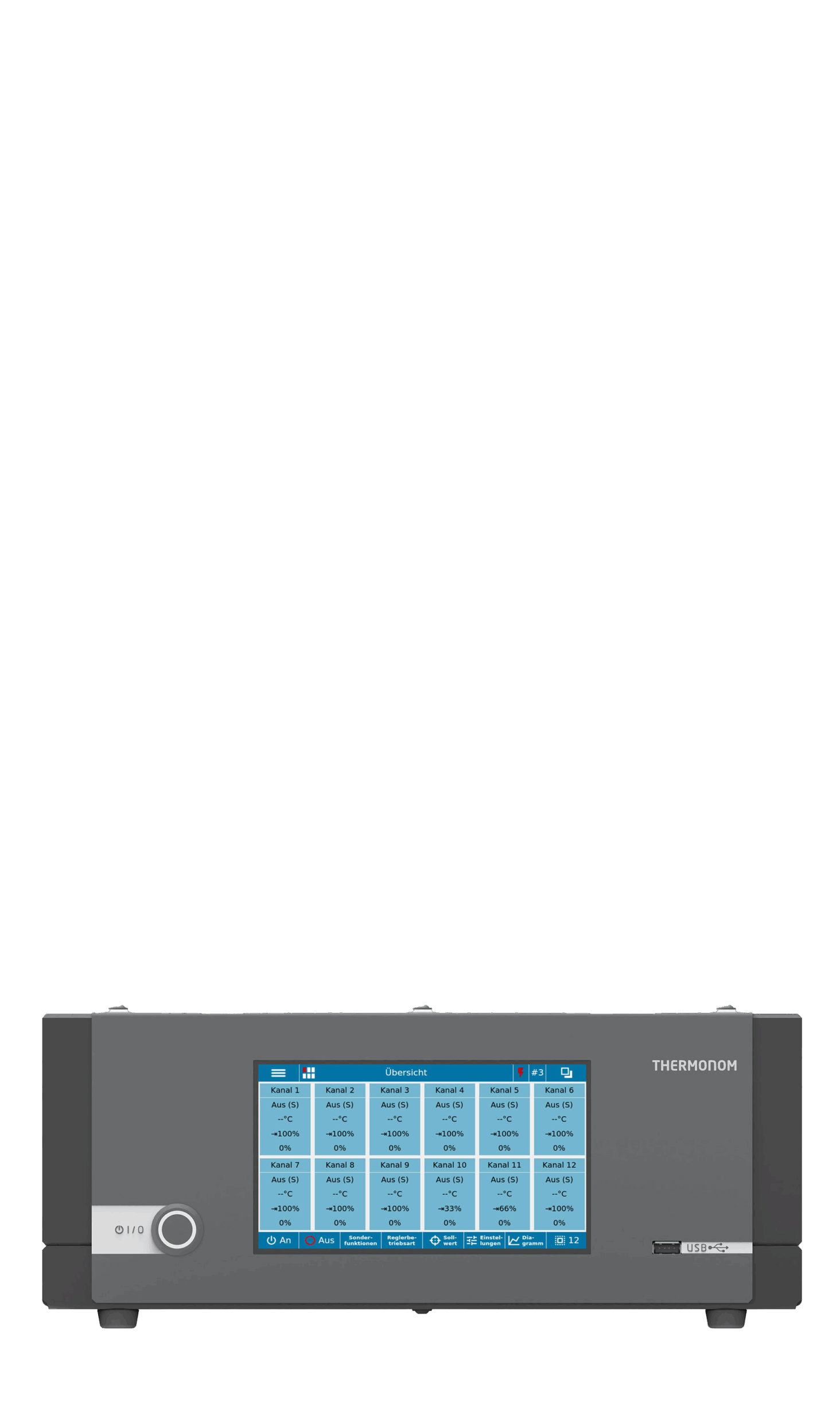
6 / 12 channels
(W x H x D)
360 X 153 X 307 mm
Overview of our service & sales partners
![]() | ![]() | ![]() |
---|---|---|
ATR Solutions GmbH In Allweiden 5a 55606 Kirn Tel.: 06752 / 123 396 0 Mail: info@atr-solutions.de Web: www.atr-solutions.de | Cintron e.K. Mollsiepen 2 58579 Schalksmühle Tel.: 02355 / 50 89 02 Mail: info@cintron-tec.de Web: www.cintron-tec.de | HEWACO Spritzgießtechnik GmbH Mauermattenstraße 8 79183 Waldkirch Tel.: 07681 / 474 389 0 Mail: info@hewaco.de Web: www.hewaco.de |
![]() | ![]() | ![]() |
---|---|---|
Jurke Engineering GmbH Dorfstraße 13 01471 Radeburg Tel.: 035208 / 39 75 20 | Kunststofftechnik Nadler GmbH & Co.KG Heinrich-Cotta-Str. 5 01324 Dresden Tel.: 0351 / 265 512 80 | Stir³ Scholz Technik in Radeberg e.Kfm. Dresdener Str. 41a 01454 Radeberg Tel.: 03528 / 229 710 1 Mail: holger.scholz@stir3.de Web: www.stir3.de |
![]() | ![]() | ![]() |
---|---|---|
Labotek Deutschland GmbH Nöllenhammerweg 10-16 D-42349 Wuppertal Tel.: 02027 / 47585 0 Mail: info@labotek-de.com Web: www.labotek.com/de | MIEBACH Kunststofftechnik e. K. Tiembacherstr. 6 90556 Cadolzburg Tel.: 09103 / 71 44 11 | HVD – Handelsvertretung Diesner UG Sorbische Straße 20 02694 Großdubrau Tel.: 03594 / 77782 Mail: office@hvd-diesner.de Web: www.hvd-diesner.de |
![]() |
---|
TST-DE Schlag 42 94481 Grafenau Tel.: 08552 / 974 77 25 Mail: info@tst-de.de Web: www.tst-de.de |
![]() |
---|
EVOMAX PLASTICS OY Realparkinkatu 4 37570 LEMPÄÄLÄ Tel.: +358 44 / 410 014 5 Mail: mauri.kautto@evomax.fi |
![]() |
---|
Kern d.o.o. OIC – Hrpelje 41 6240 Kozina Tel.: +386 5 616 50 00 Mail: info@kern.si Web: www.kern.si |
![]() |
---|
Plastline ul. Kominiarska 42AB 51-180 Wrocław Tel.: +386 5 616 50 00 Mail: info@plastline.com.pl Web: www.plastline.com.pl |
![]() |
---|
Kern d.o.o. OIC – Hrpelje 41 6240 Kozina Tel.: +386 5 616 50 00 Mail: info@kern.si Web: www.kern.si |
![]() |
---|
KNP s.r.o. Mladoboleslavska 73 19700 Praha 9 – Kbely Phone: +420 268 006 916 Mail: info@knp.cz Web: www.knp.cz |
![]() |
---|
Kunststofftechnik Nadler GmbH & Co KG Heinrich-Cotta-Str. 5 01324 Dresden Phone: 0351 / 265 512 80 |